50 Jahre gibt es die Overather Firma Fischer-Kunststofftechnik. „Wir sind immer Teil von etwa Größerem“, sagt Chef Constantin Fischer.
WirtschaftOverather Firma baut Riesen-Lüsterklemmen und Tische für die Minis
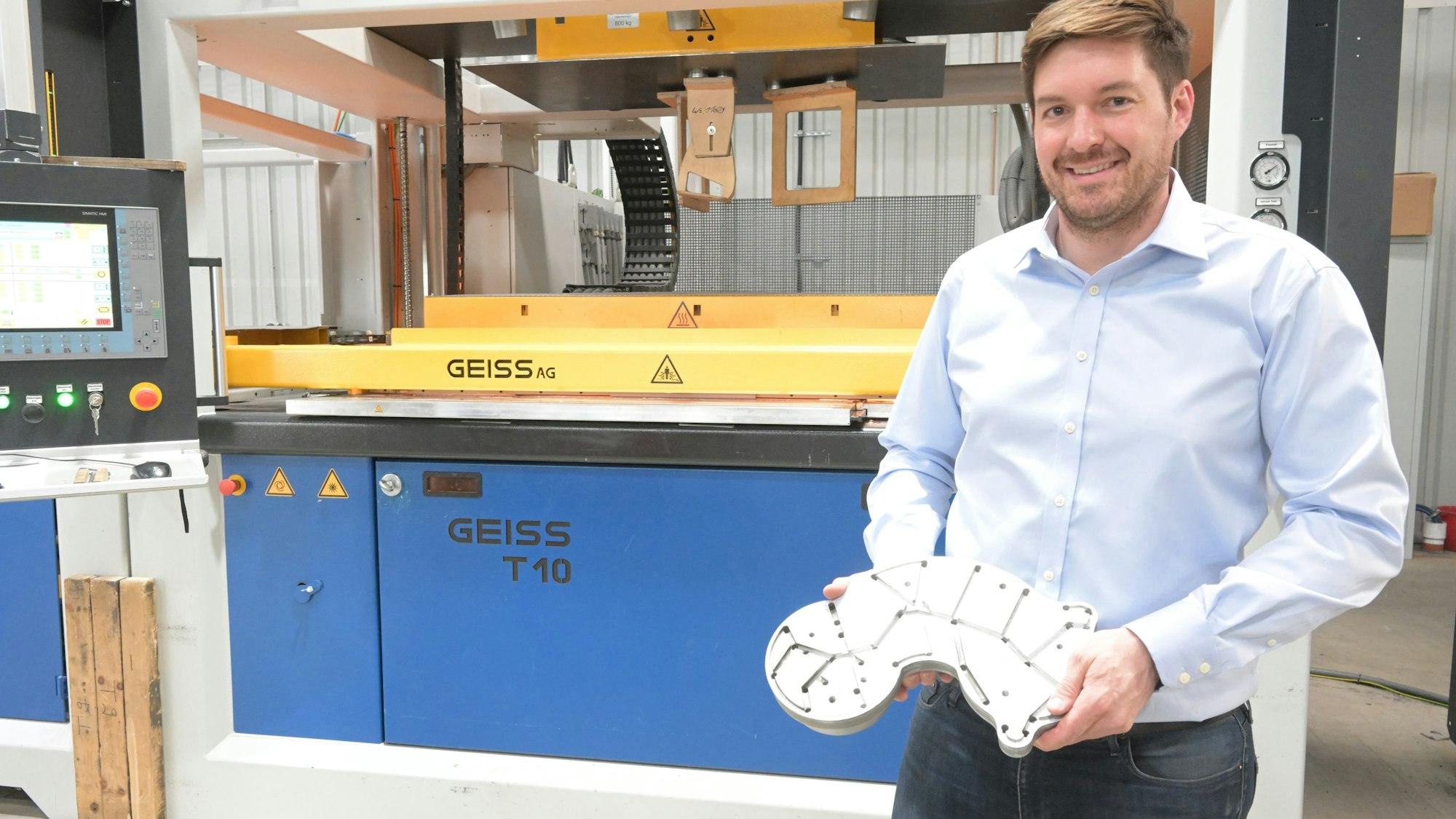
Firmenchef Constantin Fischer mit Werkzeug vor einer Thermoform-Maschine.
Copyright: Christopher Arlinghaus
Ordinäre Lüsterklemmen kennen selbst technikferne Schöngeister, sofern sie schon mal eine Lampe an der Decke angebracht haben, um den Picasso an der Wand ins rechte Licht zu setzen. Dagegen sind Lüsterklemmen für Windräder sehr viel seltener.
Beinahe mannshoch sind diese Plastikriesinnen, deren Existenzberechtigung aber mindestens genauso hoch ist wie die der kleinen Technikteilchen an der Wohnzimmerdecke. Denn sie werden immer dann gebraucht, wenn im Windpark zu Lande oder zur See ein Stromkabel zu Ende und via Kabelmuffe mit dem nächsten verbunden wird.
„Hier sieht man Fluch und Segen von Kunststoff zugleich“, sagt Constantin Fischer, Chef der Dr. Karl Gert Fischer GmbH & Co. KG in Overath. Denn die Lüsterklemmen aus dem Land der Riesinnen müssen richtig was aushalten und dürfen nicht einfach leise vor sich hin verrotten: „Der Kunststoff hat auch in hundert Jahren noch seine volle Funktionsfähigkeit.“
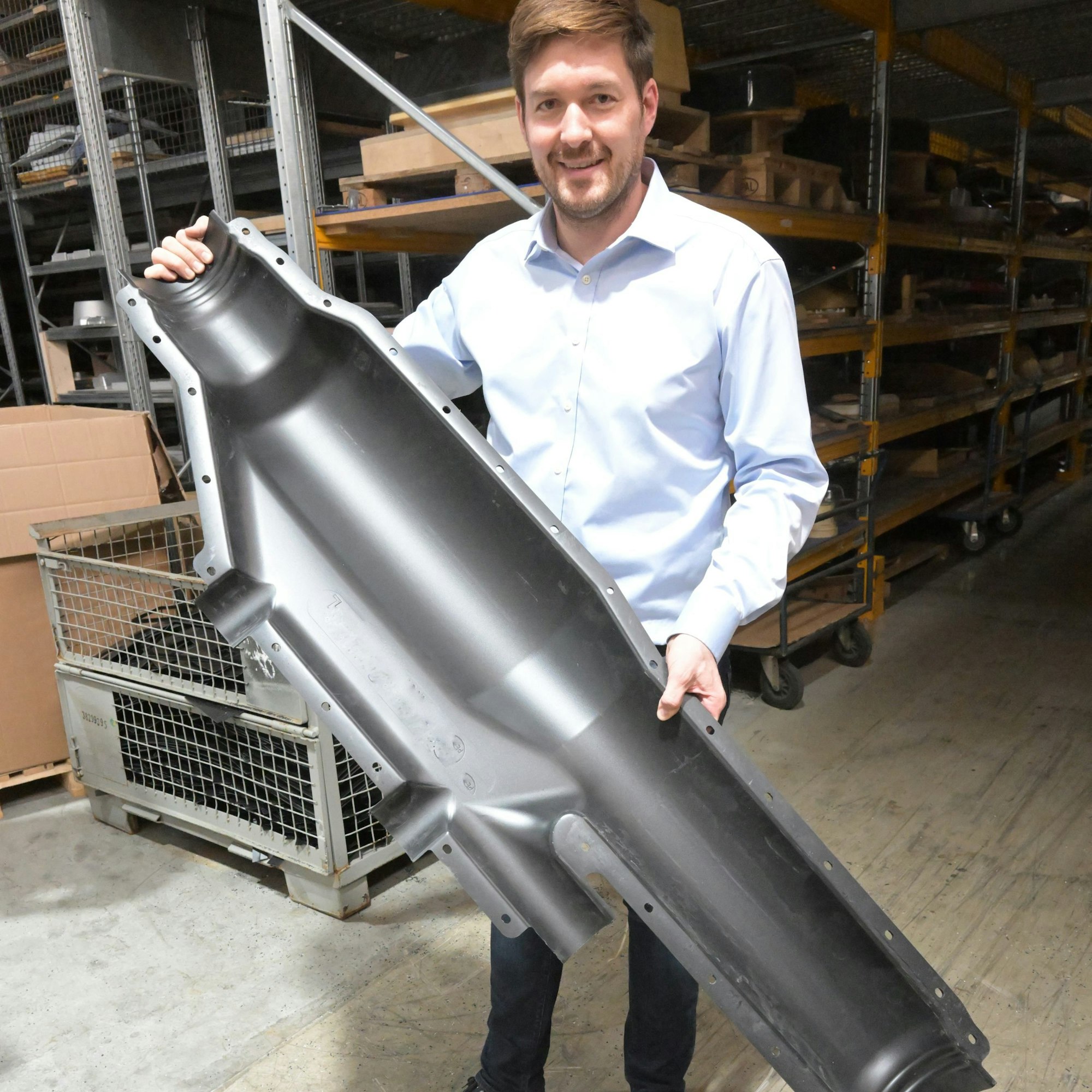
Diese Riesenlüsterklemme kommt in Windparks zum Einsatz.
Copyright: Christopher Arlinghaus
Heißt aber auch: Der Kunststoff ist, wenn man nichts unternimmt, dann eben auch noch da – genauso wie all der Verpackungsmüll, der im Meer versenkt wird. Doch ist Kunststoff eben nicht gleich Kunststoff - es kommt wie immer im Leben darauf an, was man daraus macht. Fischer: „Wir stellen ausschließlich Investitionsgüter her, wo eine lange Lebensdauer der Produkte gewünscht ist.“
Wurstthekenabdeckungen sind anders als Kindergartentische
Die Produktpalette seiner Firma mit Sitz im Ortsteil Immekeppel ist groß. Esstische für Rollstuhlfahrer gibt es zum Beispiel. Die müssen abgerundet sein, damit sich keiner daran schneidet. Oder Abdeckungen zum spätabendlichen Schutz der Wursttheke im Supermarkt– die muss nicht so rund, dafür aber lebensmittelecht sein.
Bei Tischchen für Kindergartenkinder kommt es vor allem darauf an, dass sie nicht scharfkantig brechen, und Abdeckungen für Batterien dürfen nicht brennen. Für alles gibt es Kunststoffe, die die Fischers einkaufen und dann hier bearbeiten. Die Produktpalette ist nicht nur riesengroß, sondern, wenn es der Kunde wünscht, auch sehr farbenfroh.
1979 wechselte die Firma von Köln nach Overath
Im Geschäft ist die Fischer-Kunststofftechnik seit genau seit 50 Jahren. Gegründet 1973 in Köln-Niehl von Namensgeber Dr. Karl Gert Fischer migrierte sie 1979 ins Bergische Land nach Overath-Immekeppel, weil es in Köln zu eng geworden war. Das Unternehmen wuchs langsam, aber beständig: „Praktisch für jedes Jahr haben wir einen zusätzlichen Mitarbeiter bekommen“, sagt Constantin Fischer, der 39 Jahre alte Unternehmenschef.
50 Leute sind es aktuell. Zuletzt haben sie alle zusammen den 50. Geburtstag mit einem großen Grillfest auf dem Firmengelände gefeiert. „Grillen ist gut“, sagt Fischer, „alle Leute grillen gerne und man schließt damit niemanden aus.“
Wir fertigen selbst keine Endprodukte, sondern sind immer Teil von etwas Größerem.
Beim Rundgang durch die Firma im Gewerbegebiet am Ostende von Immekeppel präsentiert der Unternehmenslenker, der durch den frühen Tod des Vaters bereits mit 26 Jahren in Führungsverantwortung kam, nicht ohne Stolz die vielen Hightech-Maschinen, mit denen die Produkte im Tiefziehverfahren hergestellt werden. „Wir fertigen selbst keine Endprodukte, sondern sind immer Teil von etwas Größerem“, sagt Fischer – wobei manche internationalen Großkunden etwas eigen seien, wenn es darum gehe, ihre Endprodukte zu benennen.
Beim Rundgang gibt es auch einen Crashkurs über die Vor- und Nachteile der verschiedenen Produktionsweisen: Wird nur eine minimale Stückzahl benötigt, kann ein 3D-Drucker den Job erledigen. Ist die Stückzahl riesig, etwa in der Automobilindustrie, ist Spritzguss gefragt, wo der Kunststoff erst geschmolzen und dann in eine Form gespritzt wird.
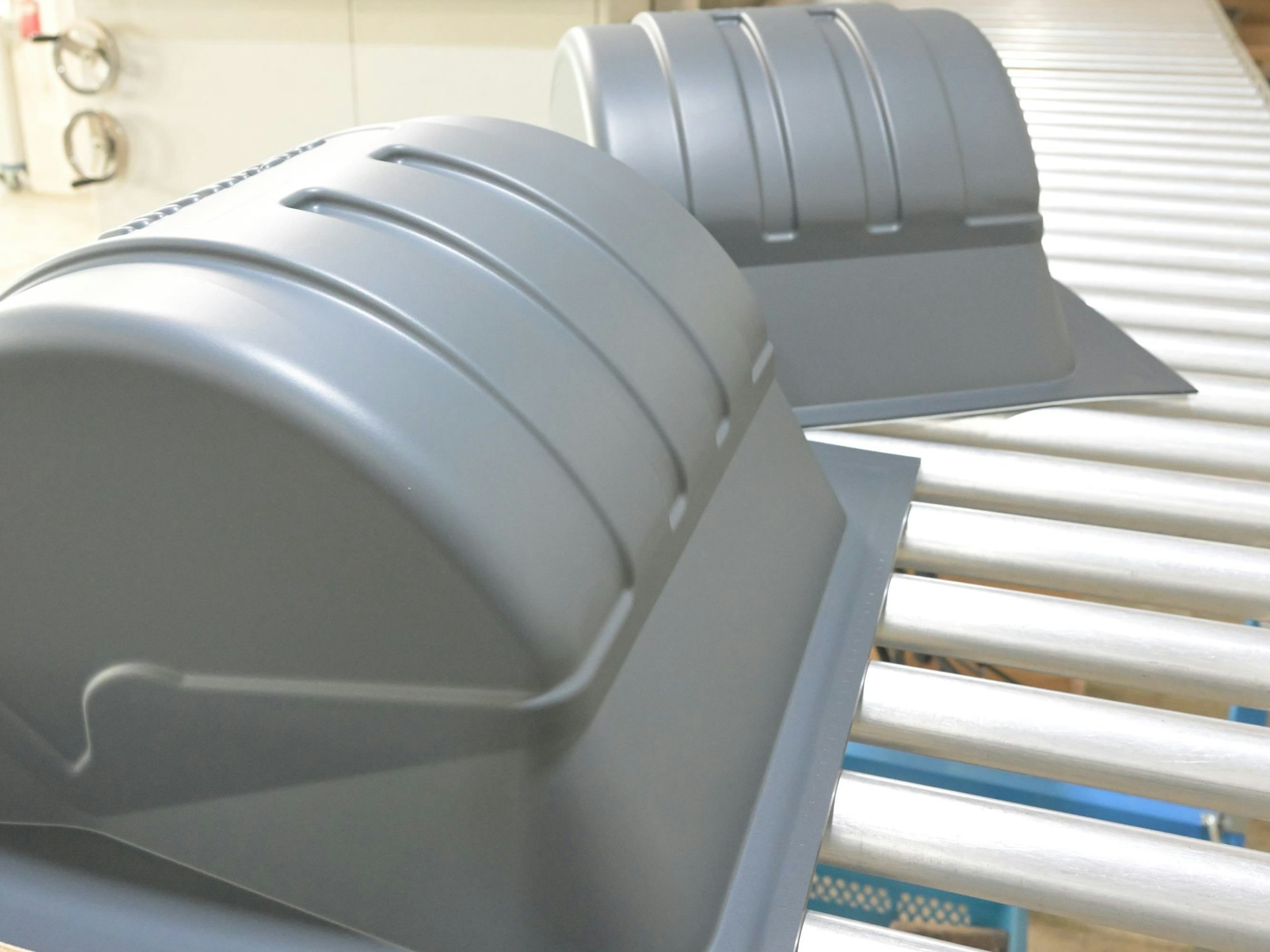
Frisch geformte Abdeckungen verlassen die Maschine.
Copyright: Christopher Arlinghaus
Aber zwischen winzig und riesig kommt die Firma Fischer: Wenn ein Unternehmen monatlich 300 Bagger oder Landmaschinen herstellt, dann bestellt es seine Deckel und Verkleidungen gerne in Immekeppel. Dort werden dann große Kunststoffplatten mit dem Gabelstapler aus dem Lager geholt und zu den bis zu einer halben Million Euro teuren Maschinen gefahren, eingespannt, erhitzt und in die gewünschte Form gebracht. Ein bisschen laut geht es schon dabei zu, die Mitarbeitenden tragen Ohrenschützer.
Anschließend werden die Formen herausgeschnitten, weiterverarbeitet, bei Bedarf zusammengefügt und mit Etiketten und Anleitungen versehen. Die Reste werden nicht weggekippt, sondern wiederverwendet.
Die Geschäftsaussichten für seine Firma sieht Fischer rosig. Das liege daran, dass immer häufiger Varianten gewünscht würden – ein Bagger in Groß, der nächste kleiner, und dann lohne sich das Thermoformen. So gut laufen die Geschäfte, dass jetzt auf dem Firmengelände eine weitere Halle gebaut werden soll. Danach würde das Unternehmen aber auch auf seinem Grundstück in Immekeppel an seine Grenzen stoßen.